26 January 2022
Containers Overboard – A Complex Issue
by Denis Speyer
A Reverse in the Trend
Since 2011 The World Shipping Council, which represents around 80% of the world’s container ship fleet capacity, has produced a report on the average number of shipping containers lost at sea per year. An annual average of 779 containers were lost from 2017 to 2019. This was against 226 million containers moved worldwide in 2019. Overall, from 2011 to 2019 there has been a decline in containers losses for each period.
However, since 2019 the trend has reversed with over 3000 containers lost overboard from seven large container vessel incidents, mostly during heavy winter weather in the North Pacific Asia/North America trade routes. The most notable were the ONE Apus which lost 1816 containers north of Hawaii en route to Japan in November 2020, and the Maersk Essen in January 2021 which lost 750 containers on passage from the USA to Asia.
Size Matters
The North Pacific losses during 2020 and 2021 mostly involved vessels built between 2010 and 2020 and of 14,000 TEU (Twenty Foot Equal Units) container capacity. These are large vessels over 360 metres in length with on-deck container bays of 20 units across and up to eight tiers high. The continuous search for economies of scale is driving the main global operators to build even larger vessels. The 2021 to 2023 delivery order book is trending to +20,000 TEU vessels at 400 metres in length, able to stack containers 24 units across.
Greater demand for container ship capacity
Recovery of inventories and consumer demand after the 2020 Covid-19 lockdowns created an unprecedented need for container capacity across the main trade routes of Asia to North America and Europe. Container vessels are at capacity both outward from Asia with full containers, and on the back haul with empty units.
Increasingly severe weather in the North Pacific and Atlantic
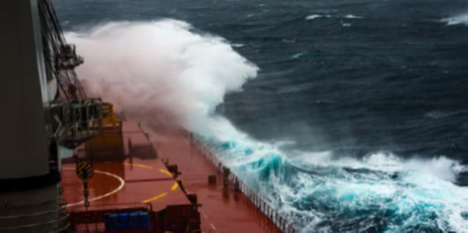
There has been a recorded increase in the number and severity of storms in the North Pacific and Atlantic Oceans due to global warming. In all seven significant container loss incidents in the North Pacific in 2020-21, heavy weather conditions triggered the loss of containers overboard. The combination of bigger vessels, loaded to full capacity, transiting ocean routes with increasing frequency and severity of heavy weather is of concern to insurers across the hull, cargo and P&I markets.
Lessons on the complexity of container losses
From June 2018 to mid-2021, Integra was closely involved in analysing the loss of 81 containers from the YM Efficiency off the east coast of Australia. Integra was appointed to investigate the cause by a collective of major cargo insurers, and then retained by lawyers representing the Australian Maritime Safety Authority (AMSA) to provide master mariner expert witness advice in its pursuit of costs from the vessel owners, incurred in the salvage operation of raising most of the containers lost to the sea.
Once again, heavy weather resulted in a stow collapse in two container bays. This was caused by weight distribution beyond the limits of the applied container securing equipment. Heavy containers were stowed over light and the stow height of both bays exceeded the limits set in the vessel’s cargo securing manual. The vessel’s cargo securing analysis software was inadequate, so the crew was unable to assess the stow against the container lashing system parameters. The two bays were loaded at the last outward Asia load port, no doubt to maximise the total container uplift with limited remaining available stowage space.
In a separate appointment, Integra was asked to analyse the loss of containers from the ANL Gippsland off Shanghai in heavy weather associated with Typhoon Lekima. In that case our conclusion was that the stability condition of the vessel was a significant contributor to the loss.
Inadequate vessel stow planning
These losses highlight the challenge of container vessel stow planning through its various stages. A carrier’s centralised vessel planning department will produce plans for each load port to maximise uplifts against the various vessel call port pairs and load and discharge requirements. There is little involvement by the vessel’s master other than checks on assumed stability and hull torsion limits for each port call. Actual container weights are not confirmed until containers are received at each load terminal. The final stow plan for each port call is computed by planners at the load terminal and presented to the vessel shortly before or sometime after its arrival. There are limited opportunities both in time and from economic constraint on any ability by the vessel master to challenge or alter a load plan as presented, particularly with vessels now trading at capacity. The responsibility for the vessel’s cargo stow, however, still rests with the master.
The growth in size of modern container vessels and their cargoes, combined with the complex forces acting on them in increasingly severe weather, against a diminishing ability of the ship’s master to assess and control the stow of containers, may require a rethink of accountability up the vessel planning chain.