29 April 2021
Luminescence imaging – The past, present and future of damage assessment of photovoltaic arrays
Assessing damage to photovoltaic array installations (PVs) can be a complex and challenging task. Installations are typically multi-modular, cover large areas and damage can be difficult to detect. Often damage will cause a reduction in efficiency or output rather than total failure. Cell-level cracks, microcracks, scratches and heat spots are difficult to identify by visual inspection with the naked eye.
The solution to damage assessment has come from the PV industry itself. PVs have a recommended design life of approximately 20 to 25 years. However, in practice, some fail in less than 10 years. Recent studies in the USA show that the average system underperforms by 6.3% compared to figures projected at financing stage. As a result, the PV industry has focused on developing technology to conduct fast and accurate testing to identify failing units. This technology is transferrable and can be used to test arrays quickly and accurately following an insured event.
Drones and infrared thermography
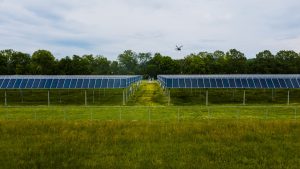
One of the more established methods of inspecting PVs with drones uses infrared thermography (IR). This well-developed and readily available technology is excellent for identifying major defects such as glass breakage, soiling (bird droppings or other), string disconnections and hotspots. However, IR is limited when it comes to micro-cracks and similar types of damage, which are commonly seen following significant wind, hailstorm or fire events.
To circumvent the limitations of IR, ongoing research has led to the development of luminescence imaging. There are two types of luminescence imaging: electroluminescence (EL) and photoluminescence (PL). Presently, only electroluminescence is being used, with photoluminescence undergoing further research and development.
Smarter electroluminescence technology
The “clever” technology used in EL is an InGaAs sensor, also referred to as an InGaAs camera. For the techies, this is essentially a two-dimensional photodiode array that detects shortwave infrared (commonly referred to as SWIR) incident light. This is collected in the form of a photo-generated charge, converted into voltage and turned into an image by off-chip electronics.
In practice, a drone is used to image the entire installation using the traditional IR technology. Once problem areas are identified from the IR images, the modules are inspected by an inspection team using EL. This involves exciting the modules with an outside source (generator) and using an InGaAs camera to produce images of the affected areas. Applying AI and machine learning, the images are reviewed and the damage identified.
From a timing perspective, the average EL team can work through approximately 1,200 modules per day. Typically, once the on-site work is completed, we expect analysis of the footage to be available within three to four weeks.
As mentioned, this technology is undergoing continuous development. Until recently, due to the interference of sunlight, EL imaging could only be undertaken in low light conditions (such as during early evenings). But, the latest InGaAs cameras compensate for sunlight “noise” and allow EL inspections to be performed in daylight. This speeds up the process and provides safer working conditions for inspection teams.
The next generation of InGaAs cameras is undergoing development and, as image acquisition rates increase,
it is anticipated that they too could become drone-mounted. This will require a corresponding improvement in the camera stabilisation gimbals fitted to drones.
Fully automated PL inspections
Research in photoluminescence is ongoing. The principle behind PL is to excite the modules using natural sunlight during the day and a laser at night. If this is achieved, and faster InGaAs cameras and improved stabilisation gimbals become available, it is anticipated that fully automated drone inspections will be possible in the future.
In our opening paragraphs we commented that, in practice, PVs exhibit failures which are not necessarily associated with insured or insurable events. EL technologies could be used to survey insured facilities, possibly every three years, to establish pre-damage baselines and define the actual pre-loss condition of an installation.
This technology is available in both the USA and Europe, with certain specialists in this sector having inspected in excess of one GW of damaged assets in the field.
In conclusion, traditional damage assessment by means of physical inspections has proved to be labour-intensive, time-consuming and fails to account for a number of damaged panels. The current use of combined IR and EL inspections of damaged PVs can present significant benefits to both insurers and PV owners in terms of time and cost savings. Although the industry has already come a long way from the physical inspections of arrays, the anticipated introduction of automated PL inspections will prove to be exceptionally beneficial in terms of time, cost saving and accuracy.
We are keenly watching the developments in this space!