1 March 2023
Power Plants: Losses during commissioning
by Derek Patterson, Deputy Managing Director, Middle East & Africa
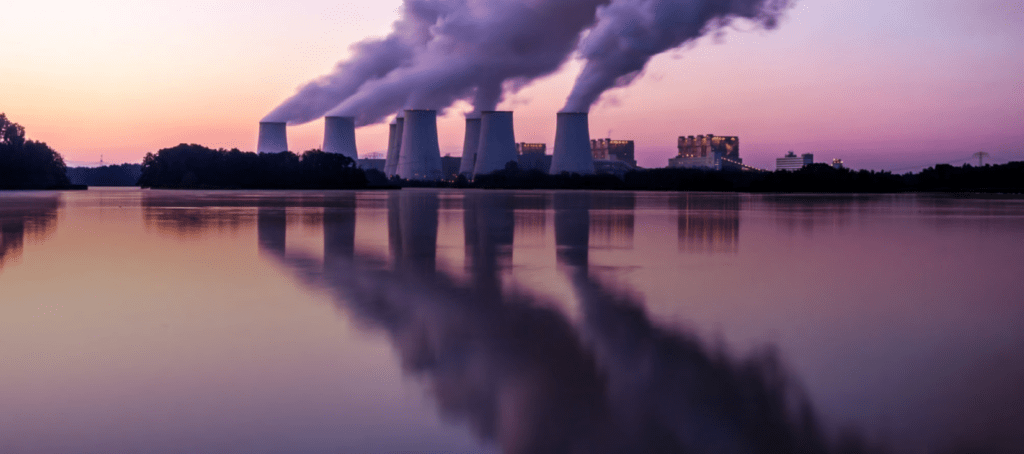
Over the years, I have experienced many costly incidents associated with major power plants. Conventional and combined cycle plants, either with steam or gas turbine primary power sources, all share a vulnerability to expensive material damage and lengthy interruption to the restart of operations.
However, whilst it is the norm to minimise risk through careful coordination of the tie-in with the power grid and fuel supply sources, the operational readiness of power plants is often delayed by incidents that arise during the commissioning and testing phases.
These stages in a plant’s life cycle are critically important from a risk perspective, yet often they are often overlooked.
This article examines four of the main causes of loss in power plants:
- Foreign object damage to gas turbines
- Contamination of pipelines
- Short circuits on electrical equipment
- Design defects
1. Foreign object damage (FOD)
The leading culprits of FOD damage are loose debris or unsecured nuts within the filter / air intake system. The filter house and air intake system for gas turbines should always be doublechecked for debris. All kinds of metal object, from the heads of pop rivets to small tools, can be left in the air intake system. Ingestion into the engine can result in a very expensive noise within the compressor, and chunks knocked off the fixed and rotating blades. If this happens, the removal of top casings becomes necessary to effect repairs.
Another typical scenario is where nuts from bolts within the ducting are not spot welded after tightening. These can loosen and become sucked into the engine. So, it is especially important that the insured checks every nut is tack-welded.
2. Contamination
Contamination is the second most common cause of loss. It can result from the inadequate flushing of cooling water, lubricating oil and (in some cases) pneumatic systems. Typically, welding debris, plastic or other waste is not flushed properly from pipes and valves. The waste material blocks filters, reduces flow and pressure, and damages pumps, valves, bearings and other components. Sometimes, debris can block a pump and cause significant damage within just a few minutes.
Other examples:
- Gas turbine fuel piping – caused by weld or corrosion debris, especially if old pipes are used at a higher flowrate than before, or after a long period of non-use. I have seen several incidents of severe hot section damage from rust carryover, and witnessed tools and large pieces of steel left in pipework, and purging not done adequately.
- Air piping – especially purge air systems for the turbine and the air filter.
- Boilers – corrosion, tools, weld debris and dirt left in boiler pipework are all potentially harmful.
Boilers are especially prone due to the large quantity of internal pipework. - Condenser leakage – contaminating the boiler and turbine, especially in seawater-cooled condensers. This is not always taken seriously enough at commissioning stage.
- Misconnected pipework – I have seen drains connected to supply pipes and high-pressure pipes connected to low-pressure pipes. Proper checking should prevent this happening, but incidents still occur.
- Contamination – in my experience, the contamination of oil, fuel, water, steam, air and fuel piping and ducting are the most common and avoidable issues for turbomachinery during commissioning.
The operator should always have a system in place for checking the contractor on all pipe system flushing procedures.
3. Short circuits
Short circuits are the root of many problems. Whilst a short circuit in a single component can normally be repaired fairly easily, it can often create a cascade of faults that affects multiple components. An especially vulnerable area is the backup system for emergency oil pumps and electrical protection. If an emergency pump circuit does not kick-in, entire systems could suffer serious harm (e.g. every bearing on a generator could be damaged). A protection-system failure can also trigger an expensive series of further failures.
The biggest areas of electrical risk are the cable terminations in the generator step-up transformers and other transformers. It is crucial that these terminations are completed by certified technicians qualified to work on specific termination types.
Design defects
These can vary from major turbine defects to minor design faults:
- Poorly designed air filter systems
- Fundamental defects in turbine design (in this case, not much can be done other than monitor closely during initial operation)
- Badly supported or connected oil or gas pipework, leading to a fire
- Purging with a flammable, heavier-than-air gas which gathers in drains
Other turbine issues include
- Malsynchronisation – from the incorrect connection of cables
- Misalignment – sometimes due to the combined effect of multiple causes. Likely contributors could be bad workmanship, inadequate (moving) foundations, low-quality design or poor insulation of bearings and casings causing thermal movement
In conclusion, many of the above risk factors can be eliminated or reduced by improved awareness and better coordination between the contractors, commissioning team and operations management. This
is critical throughout the construction and commissioning of plants, and while planning and testing the appropriate procedures. We must also remember that the above does not address the risk of natural perils, with the most significant of these being flooding during or shortly after commissioning and testing.